Prozessoptimierung im Evakuierungsmanagement
Facility Management: Evakuierungen » Strategie » Prozessoptimierung
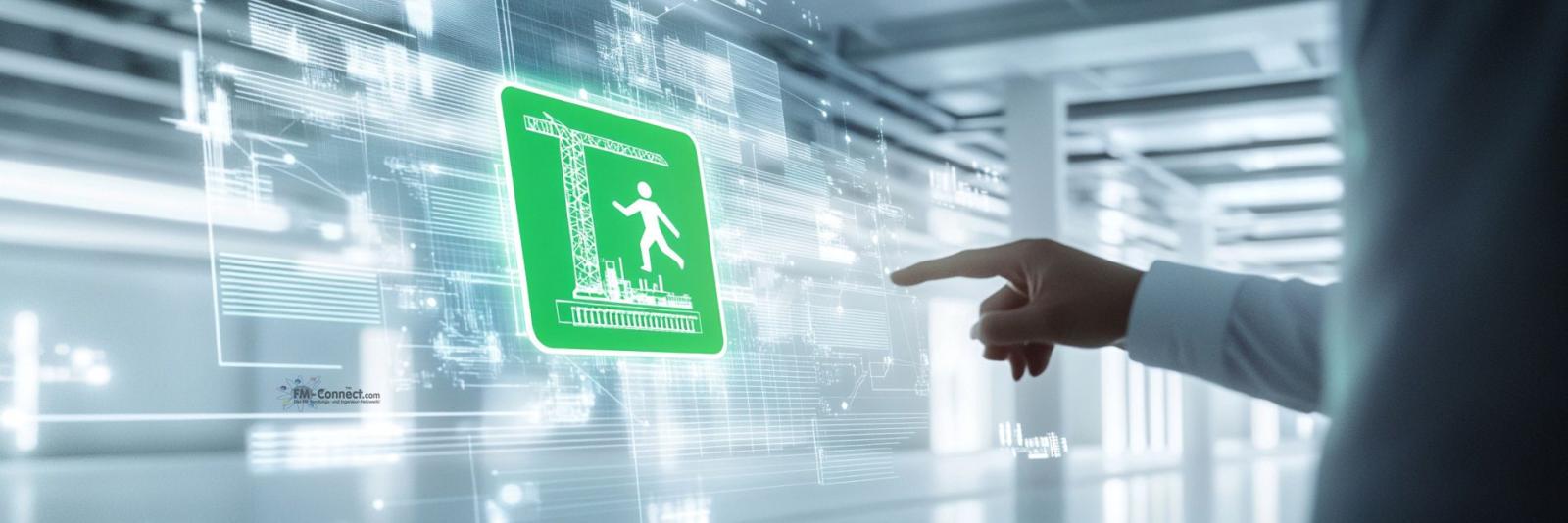
Prozessoptimierung im Evakuierungsmanagement
Unternehmen stehen vor komplexen Gefahrenlagen wie Bränden, Unfällen mit Gefahrstoffen oder technischen Störungen, die eine rasche Evakuierung erfordern. Ein wirkungsvolles Evakuierungsmanagement hat strategisch das oberste Ziel, im Notfall Menschenleben zu schützen und Verletzungen zu vermeiden. Darüber hinaus trägt es zur Sicherstellung der Geschäftskontinuität bei, indem Ausfallzeiten minimiert und Sachschäden begrenzt werden. Die Zieldefinition sollte daher klare Schutzziele umfassen, etwa maximale Evakuierungszeit, Vollzähligkeit der evakuierten Personen und keine Unfälle während der Evakuierung. Diese Ziele müssen mit den übergeordneten Unternehmensstrategien (Arbeitssicherheit, Risikomanagement und Facility Management) in Einklang stehen. Ein strategischer Rahmen beinhaltet auch die Verankerung der Evakuierungsplanung in der Sicherheitskultur des Betriebs – von der Geschäftsleitung bis zum einzelnen Mitarbeitenden. Letztlich ist Prozessoptimierung in diesem Kontext nicht Selbstzweck, sondern ein Beitrag zu einer proaktiven Sicherheitsstrategie, die rechtliche Vorgaben erfüllt und Vertrauen bei Mitarbeitern sowie Behörden schafft.
Es bildet der rechtliche Rahmen einen verbindlichen Mindeststandard, der in jedem Evakuierungskonzept erfüllt sein muss – von freien Fluchtwegen über beschilderte Ausgänge bis zu regelmäßigen Übungen. Die genannten Normen und Regeln (ArbStättV, ASR A2.3, DIN ISO 23601, DIN EN ISO 7010, DIN 14096 etc.) definieren detailliert das „Wie“ einer sicheren Evakuierung: angefangen bei baulichen Vorgaben (Anzahl, Breite, Beleuchtung von Notausgängen) bis hin zu organisatorischen Maßnahmen (Inhalt von Plänen, Unterweisungspflichten). Für leitende Facility Manager bedeutet dies, stets auf dem Laufenden zu bleiben, da Gesetze und Regeln sich fortentwickeln. Die Einhaltung dieser Vorgaben ist nicht nur eine lästige Pflichterfüllung, sondern bildet die Grundlage für ein zuverlässiges Evakuierungsmanagement. Nur wer die Norm verlangt, dauerhaft erfüllt und idealerweise übertrifft, schafft ein Umfeld, in dem im Ernstfall alle Personen sicher und geordnet gerettet werden können – und in dem ein Unternehmen seiner Verantwortung für Mitarbeiter und Umwelt gerecht wird.
Analyse bestehender Prozesse und Schwachstellen
Prozesse und Schwachstellen
Zu Beginn jeder Optimierung steht die Analyse des Status quo der Evakuierungsprozesse. Dies umfasst die Auswertung bestehender Notfall- und Alarmpläne, vergangener Evakuierungsübungen und Beinahevorfälle. Typische Schwachstellen lassen sich in vielen Betrieben erkennen: Häufig sind unklare Kommunikationswege und unklare Alarmierungsprozesse ein Problem – Mitarbeiter wissen im Ernstfall nicht genau, wie sie sich verhalten sollen oder wer Anweisungen gibt. Ebenfalls verbreitet sind blockierte Fluchtwege, etwa wenn Lagerware, Paletten oder Maschinen „kurzzeitig“ vor Notausgängen abgestellt werden. Solche Hindernisse können im Panikfall tödliche Verzögerungen verursachen. Auch fehlende oder unzureichende Kennzeichnungen (verblasste oder normwidrige Fluchtwegschilder) und mangelhafte Notbeleuchtung gehören zu den häufigsten Mängeln. In einigen Fällen sind Evakuierungspläne veraltet – Umbauten oder geänderte Abteilungen wurden nicht eingepflegt, was im Ernstfall zu Irrwegen und Chaos führen kann. Weitere Schwachstellen speziell in Industriebereichen umfassen hohe Brandlasten (brennbare Materialien) entlang von Fluchtwegen, Automatiktüren, die sich im Notfall nicht öffnen, sowie Stolperstellen an Schwellen und Übergängen. Nicht zuletzt wird in der Analyse oft deutlich, dass Schulungsdefizite bestehen: Vielen Mitarbeitern sind die Evakuierungsrouten oder Sammelstellen nicht vertraut, insbesondere neu eingestellte oder in Nachtschicht arbeitende Beschäftigte.
Industriespezifische Herausforderungen: Industriebetriebe weisen besondere Risiken auf, die bei der Prozessanalyse berücksichtigt werden müssen. In Produktionshallen mit Maschinenparks können laufende Anlagen und Fahrzeuge (z. B. Gabelstapler) die Evakuierung behindern – hier gilt es, Verfahren zum sicheren Herunterfahren gefährlicher Anlagen im Notfall festzulegen. Bei Umgang mit Gefahrstoffen (Chemikalien, Gase) kann eine Evakuierung komplexer sein, da ggf. erst Warnanlagen (Gasdetektoren, Löschanlagen) auslösen und Mitarbeiter persönliche Schutzausrüstung anlegen müssen. Es besteht zudem die Gefahr, dass ein geordnetes Verlassen durch Schutzeinrichtungen (z. B. Schleusen in Reinräumen oder Werksicherheitsschleusen) verlangsamt wird – diese Prozesse sollten vorab optimiert oder im Alarmfall überbrückt werden. Schichtbetrieb und Personalschwankungen stellen ein weiteres Risiko dar: In Nachtschichten ist weniger Personal vor Ort, gleichzeitig müssen aber auch zu ungewöhnlichen Zeiten alle Anwesenden erreicht und geführt werden. Die Anzahl ausgebildeter Evakuierungshelfer und Anwesenden-Listen müssen deshalb schichtübergreifend ausreichend sein. Schließlich erfordert auch eine mögliche Sprachbarriere Berücksichtigung – in international besetzten Teams müssen Alarmierungen mehrsprachig oder mit klaren Signalen erfolgen. All diese Erkenntnisse aus der Analysephase fließen in die Definition von Handlungsfeldern für die Optimierung ein. Es empfiehlt sich, die identifizierten Schwachstellen nach Priorität (Gefährdungspotenzial) zu ordnen, um anschließend systematisch Verbesserungsmaßnahmen abzuleiten.
Beispiel: Deutlich gekennzeichnete Sammelstellen außerhalb des Gefahrenbereichs sind essentieller Bestandteil eines Evakuierungsprozesses. Fehlende oder unklare Ausschilderungen von Sammelpunkten zählen zu den häufigen Schwachstellen und verzögern die Vollständigkeitskontrolle.
Methodische Ansätze zur Optimierung
Lean Management: Die Prinzipien des Lean Management zielen darauf ab, Verschwendung in Prozessen zu eliminieren und Abläufe schlanker und schneller zu gestalten. Übertragen auf Evakuierungsprozesse bedeutet dies z. B., unnötige Schritte oder Verzögerungen im Alarmierungs- und Räumungsablauf zu beseitigen. Eine Wertstromanalyse des Evakuierungsprozesses kann helfen, jeden Abschnitt vom Alarm bis zur Rückmeldung der Vollzähligkeit zu durchleuchten. Identifizierte „Verschwendungen“ könnten etwa zu lange Reaktionszeiten der Mitarbeiter sein (hier helfen Standards und Übungen, um die Reaktionszeit zu verkürzen) oder Umwege wegen ungünstiger Fluchtwegführungen (hier können bauliche Anpassungen oder bessere Beschilderung Abhilfe schaffen). Auch 5S-Prinzipien – Ordnung und Sauberkeit am Arbeitsplatz – unterstützen die Evakuierung, da sie sicherstellen, dass Wege frei sind und Notausgänge nicht verstellt werden. Lean Management fördert zudem eine Kaizen-Kultur der kontinuierlichen Verbesserung, in der Mitarbeiter angehalten sind, Sicherheitsprozesse fortlaufend zu hinterfragen und zu optimieren.
Six Sigma: Während Lean den Fokus auf Schnelligkeit legt, konzentriert sich Six Sigma auf Qualität und Fehlerreduktion in Prozessen. Im Evakuierungsmanagement bedeutet das, den Räumungsprozess so robust zu gestalten, dass er auch unter variierenden Bedingungen zuverlässig funktioniert. Mit Six Sigma-Methodik (DMAIC: Define, Measure, Analyze, Improve, Control) kann man z. B. die Evakuierungszeiten über mehrere Übungen messen und statistisch auswerten, um Ausreißer und Ursachen für Verzögerungen zu identifizieren. Ein Defect im Sinne von Six Sigma wäre hier etwa eine Person, die im Alarmfall nicht rechtzeitig am Sammelplatz eintrifft – die Ursachen (etwa unklarer Alarmton in lauter Produktionsumgebung, Person hat Alarm nicht gehört) werden analysiert und Gegenmaßnahmen entwickelt. Six Sigma fördert auch die Standardisierung: Klare, dokumentierte Notfallprozesse reduzieren Varianz im Verhalten der Belegschaft. Methoden wie 5-Why-Analysen oder Ursachen-Wirkungs-Diagramme helfen, tieferliegende Schwachstellen zu ergründen (beispielsweise warum ein bestimmter Bereich des Werks immer länger zur Evakuierung braucht als andere). Insgesamt erhöhen Lean und Six Sigma die Prozesseffizienz und -qualität, was im Notfall direkte Auswirkungen auf die Sicherheit hat.
Digitale Tools: Die Digitalisierung bietet heute eine Fülle von Möglichkeiten, Evakuierungsprozesse effektiver zu gestalten. Automatische Brandmeldeanlagen (BMA) und Sprachalarmanlagen können etwa einen Brand früh erkennen und durch klar verständliche Durchsagen gezielt zur Evakuierung auffordern. Moderne Evakuierungsmanagement-Software ermöglicht die Echtzeit-Verfolgung des Evakuierungsstatus: Zum Beispiel erfassen Zugangs- und Zeiterfassungssysteme automatisch, welche Mitarbeiter und Besucher sich im Gebäude befinden. Bei Alarm kann eine dynamische Evakuierungsliste alle anwesenden Personen auflisten und aktualisieren, sobald jemand das Werksgelände verlässt. Verantwortliche erhalten so am Sammelplatz via Tablet oder Smartphone jederzeit einen aktuellen Überblick, wer noch fehlt. Gedruckte Anwesenheitslisten gehören der Vergangenheit an – sie wären in einem großen Betrieb oft schon veraltet, sobald sie ausgedruckt sind. Weitere digitale Hilfsmittel sind Alarm-Apps oder SMS-Benachrichtigungen, mit denen neben Sirenen auch stille Alarmierungswege beschritten werden (wichtig z. B. in lauten Produktionsumgebungen oder bei Angriffsszenarien, in denen kein allgemeiner Lärm erzeugt werden soll). IoT-Sensorik kann genutzt werden, um Türen automatisch zu entriegeln, Lüftungen zu steuern oder zu detektieren, ob Räume wirklich leer sind. EDV-gestützte Systeme erlauben ferner die lückenlose Protokollierung von Übungen und echten Vorfällen sowie deren Auswertung, was gezielte Verbesserungen stark erleichtert. Insgesamt führen digitale Tools zu einer schnelleren Alarmierung, besseren Informationslage und geringeren organisatorischen Fehlern im Notfall.
Künstliche Intelligenz (KI): KI-Anwendungen im Evakuierungsmanagement stehen zwar noch am Anfang, zeigen aber großes Potenzial. Durch Machine-Learning-Modelle können beispielsweise Prognosen erstellt werden, wie sich Menschenströme in einer Paniksituation bewegen, um Engpässe frühzeitig zu erkennen. In komplexen Anlagen ist denkbar, dass KI in Echtzeit die sichersten Evakuierungsrouten berechnet – unter Einbezug der Gefahrensensors (z. B. Ausbreitung von Rauch oder Chemikalien) – und den Personen personalisierte Anweisungen gibt. Erste Lösungen setzen etwa KI-gestützte Kommunikation ein: Automatisierte Anruf- oder Messaging-Systeme können im Notfall Anweisungen an Mitarbeiter verbreiten, die je nach Standort der Person unterschiedliche Fluchtrouten empfehlen. Ebenso kann KI helfen, Falschalarme von echten Notfällen zu unterscheiden, um unnötige Evakuierungen zu vermeiden. In der Prävention analysiert KI große Datenmengen (Beinaheunfälle, vergangene Evakuierungen) und erkennt Muster, die auf potenzielle Risiken hindeuten. Langfristig könnte KI so eine adaptive Evakuierungsplanung ermöglichen, die sich dynamisch an die jeweilige Lage anpasst. Bei aller Euphorie ist jedoch wichtig, KI-Lösungen stets gründlich zu testen und mit Expertenwissen zu kombinieren, da Fehlentscheidungen einer KI in Evakuierungssituationen gravierende Folgen hätten.
Simulation und Modellierung: Die Simulation von Evakuierungen hat sich als wertvolles ingenieurmäßiges Verfahren etabliert, um Evakuierungspläne zu überprüfen und zu optimieren. Mit speziellen Evakuierungssoftware-Tools (z. B. Pathfinder, FDS+Evac, PedGo) können realitätsnahe Szenarien im Computer durchgespielt werden. Dabei werden Personenströme modelliert, inklusive individueller Parameter wie Gehgeschwindigkeit, Reaktionszeit, Verhalten bei Türstau etc., um den zeitlichen Ablauf einer Räumung zu simulieren. Solche Simulationen liefern wichtige Kennzahlen, etwa Entfluchtungszeiten für verschiedene Gebäudebereiche, und decken potentielle Stauzonen auf, in denen es zu Engpässen kommen könnte. Auf dieser Basis können bauliche, technische oder organisatorische Maßnahmen schon vorab getestet werden – z. B. wie sich eine zusätzliche Fluchttür oder geänderte Möblierung auf die Evakuierungsdauer auswirkt. Insbesondere bei großen Industrieanlagen oder Sonderbauten mit vielen Personen sind Simulationen hilfreich, um nachzuweisen, dass die vorhandenen Fluchtwege für die Belegschaft ausreichen. Sie erlauben es auch, Worst-Case-Szenarien gefahrlos durchzuspielen, die man als reale Übung kaum darstellen kann (etwa den Ausfall eines zentralen Ausgangs oder das Zusammentreffen mehrerer Gefahren). Simulationsergebnisse werden von Behörden und Sachverständigen zunehmend anerkannt, z. B. um bei Abweichungen von Bauvorschriften eine ausreichende Sicherheit ingenieurmäßig nachzuweisen. Allerdings erfordert die Modellerstellung Fachwissen und Sorgfalt – falsche Annahmen oder ungenaue Daten können irreführende Resultate liefern. In jüngster Zeit ermöglicht die Integration von Building Information Modeling (BIM), Simulationsmodelle direkt aus digitalen Gebäudedaten abzuleiten, was den Aufwand reduziert. Insgesamt sind Simulationen ein mächtiges Werkzeug, um den Evakuierungsprozess im virtuellen Raum zu optimieren, bevor reale Leben davon abhängen.
Umsetzung: Change Management, Schulung, Verantwortlichkeiten
Die besten Konzepte und Methoden nützen wenig, wenn sie nicht adäquat umgesetzt werden. Evakuierungsprozesse berühren etablierte Verhaltensweisen und Organisationsstrukturen – folglich ist Change Management gefragt. Zunächst muss die Unternehmensleitung klar kommunizieren, dass Sicherheit Vorrang hat und die Optimierung des Evakuierungsmanagements eine hohe Priorität besitzt. Ein interdisziplinäres Projektteam (Facility Management, Arbeitssicherheit, Produktionsleitung, Betriebsrat etc.) kann die Umsetzung begleiten und Betroffene einbinden, um Akzeptanz zu schaffen. Widerstände der Belegschaft (z. B. Unmut über häufigere Evakuierungsübungen oder neue Vorschriften) sollten durch Transparenz und Aufklärung begegnet werden: Wenn Mitarbeitern die Sinnhaftigkeit von Änderungen – etwa das Entfernen lange genutzter Abkürzungen wegen Gefährdung im Notfall – erklärt wird, steigt die Bereitschaft mitzuziehen. Praktisch empfiehlt es sich, Änderungen zunächst in kleinen Einheiten oder Pilotbereichen zu testen und Erfolge sichtbar zu machen (Quick Wins), bevor sie unternehmensweit ausgerollt werden.
Ein zentrales Element der Umsetzung ist die Schulung aller Beteiligten. Gemäß dem Motto "Jede Person im Betrieb ist ein Teil des Evakuierungsprozesses" müssen alle Beschäftigten regelmäßig unterwiesen werden. Bereits neue Mitarbeiter erhalten idealerweise am ersten Tag eine Einführung in die Alarm- und Fluchtwege. Neben allgemeinen Unterweisungen sind praktische Übungen entscheidend: Nur wer einmal tatsächlich den nächsten Notausgang genommen und die Sammelstelle aufgesucht hat, wird im Ernstfall ruhig und routiniert handeln. Übungen sollten mindestens jährlich stattfinden (viele Betriebe üben halbjährlich) – ASR A2.3 sieht sogar vor, dass basierend auf den Flucht- und Rettungsplänen jährlich eine Evakuierungsübung durchgeführt wird. Wichtig ist, Übungen realitätsnah zu gestalten (z. B. mit angekündigtem Teil-Ausfall eines Ausgangs oder simulierten Verletzten), ohne die Sicherheit zu kompromittieren. Die Evakuierungshelfer und sonstige Notfall-Verantwortliche benötigen darüber hinaus vertiefte Ausbildungen. Diese können sich an Richtlinien wie VDI 4062 orientieren und beinhalten z. B. den Umgang mit Feuerlöschern, Menschenführung in Paniksituationen und Besonderheiten des eigenen Betriebs. Schulungen sollten auch Schichtarbeiter und temporär Anwesende (Werkvertragsnehmer, Besucher) einschließen – entweder indem für alle Schichten separate Unterweisungen erfolgen oder indem z.B. Nachts im kleineren Rahmen geübt wird. Insgesamt schafft nur permanente Bildung und Übung die nötige Handlungssicherheit bei allen Beteiligten.
Klare Verantwortlichkeiten sind das Rückgrat eines funktionierenden Evakuierungsmanagements. Bereits in der Alarm- und Evakuierungsplanung ist festzulegen, wer im Notfall welche Aufgabe übernimmt. Hierzu gehört die Benennung eines übergeordneten Evakuierungsleiters (oft der Sicherheitsingenieur oder Facility Manager), der im Ereignisfall die zentrale Koordination am Sammelplatz übernimmt und Verbindung zu externen Einsatzkräften hält. Ebenso müssen ausreichend Evakuierungshelfer ernannt werden – in Bürogebäuden als Stockwerkshelfer, in Industriebetrieben z.B. pro Hallensektion oder Schicht. Diese Helfer unterstützen beim Auslösen des Alarms, leiten die Räumung an und kontrollieren gefährdete Bereiche. Bei der Festlegung der Anzahl ist großzügig zu planen: Es sollten genug Evakuierungshelfer ausgebildet sein, um Urlaub, Krankheit oder Schichtwechsel abzudecken. In einem Schichtbetrieb muss also pro Schicht eine ausreichende Anzahl verfügbar sein. Die Aufgaben der Helfer umfassen u.a., Räume systematisch abzugehen (soweit eigene Sicherheit gewährleistet ist), Personen mit Einschränkungen gezielt zu helfen und an Treppen oder Ausgängen geordnete Abläufe sicherzustellen. Verantwortlichkeiten müssen ferner für technische Maßnahmen geklärt sein: Wer betätigt z.B. eine manuelle Not-Aus-Steuerung für Maschinen, wer stellt gefährliche Anlagen ab, wer übernimmt Erste Hilfe an der Sammelstelle etc. Diese Zuständigkeiten gehören in Notfallhandbücher oder die Brandschutzordnung des Betriebs und sollten allen bekannt sein. Auch externe Partnerschaften sind Teil der Verantwortungskette: So ist vorab festzulegen, wie die Zusammenarbeit mit der Feuerwehr und anderen Rettungskräften erfolgt, wer diese alarmiert und wer sie bei Eintreffen einweist. Unternehmen stimmen ihre Pläne idealerweise regelmäßig mit den örtlichen Behörden ab und führen gemeinsame Übungen durch. Letztlich entsteht durch klar verteilte Rollen – vom Top-Management bis zum Evakuierungshelfer vor Ort – ein strukturiertes Zusammenspiel, das im Krisenmoment reibungslos greifen soll.
Evaluation und kontinuierliche Verbesserung
Ein optimierter Evakuierungsprozess bleibt nur dann wirksam, wenn er kontinuierlich überprüft und verbessert wird. Daher folgt auf jede Übung und jeden Ernstfall eine Evaluation: Alle relevanten Ereignisse und Beobachtungen werden erfasst (z. B. Beginn des Alarms, Räumungsdauer für einzelne Bereiche, besondere Vorkommnisse) und dokumentiert. Eine ausführliche Nachbereitung von Evakuierungsübungen ist entscheidend, um aus ihnen zu lernen. Dazu gehört, in einer Nachbesprechung mit Evakuierungshelfern und ausgewählten Mitarbeitern die Ablaufprotokolle durchzugehen: Wurden die Räumungsziele erreicht? Wo traten Verzögerungen oder Unsicherheiten auf? Gab es unerwartete Probleme (etwa jemanden, der den Alarm nicht hörte, oder Schwierigkeiten bei der Zählung am Sammelplatz)? Solche Schwachstellenanalysen ermöglichen es, gezielte Verbesserungsmaßnahmen zu entwickeln. Beispielsweise könnte sich herausstellen, dass ein Alarmton in der Produktionshalle überhört wurde – Abhilfe: zusätzliche Blitzleuchten installieren. Oder die Auswertung ergibt, dass die Evakuierung einer bestimmten Werkshalle deutlich länger dauerte als geplant – Abhilfe: zusätzliche Fluchttüren prüfen oder Wege räumen. Alle Änderungen sollten in den Evakuierungsunterlagen und Plänen fortgeschrieben und an die Beschäftigten kommuniziert werden.
Die kontinuierliche Verbesserung ist idealerweise im Rahmen eines PDCA-Zyklus (Plan-Do-Check-Act) verankert. Planen: Auf Basis der Evaluationsergebnisse werden Optimierungen geplant und Verantwortlichkeiten zur Umsetzung festgelegt. Durchführen: Die Maßnahmen (z. B. neue Beschilderung, geänderte Alarmsequenzen, extra Schulungen) werden implementiert. Prüfen: Bei der nächsten Übung oder internen Audit wird kontrolliert, ob die Änderung den gewünschten Effekt hatte (etwa kürzere Evakuierungszeit oder weniger Verwirrung). Handeln: Bei Erfolg wird die Maßnahme standardisiert; bei Misserfolg werden weitere Anpassungen vorgenommen. Somit entsteht ein Regelkreis des Lernens, der das Evakuierungsmanagement lebendig hält. Zusätzlich sollten Kennzahlen (KPI) etabliert werden, um Fortschritte messbar zu machen – z. B. durchschnittliche Evakuierungsdauer, Prozentsatz der Mitarbeiter, die die Sammelstelle innerhalb von X Minuten erreichen, Ergebnisse von Wissenstests in Unterweisungen, etc. Auch Beinaheunfälle im Evakuierungsablauf (wie z.B. fast gestürzte Personen bei einer Übung) verdienen Beachtung, da sie wertvolle Hinweise liefern, bevor etwas Schlimmeres passiert. Ein weiterer Aspekt der Evaluation ist der Blick nach außen: Die Teilnahme an branchenspezifischen Netzwerken oder der Austausch mit Fachverbänden (z. B. Erfahrungen anderer Werkleiter, Veröffentlichungen der DGUV) gibt Einblicke in Best Practices und neue Technologien. Gerade für Leiter im Facility Management lohnt es sich, die Entwicklungen – etwa neue Normen, Simulationsmethoden oder KI-Tools – im Auge zu behalten und zu bewerten, ob sie für das eigene Evakuierungskonzept nutzbringend sind. Letztlich signalisiert ein konsequent gelebter Verbesserungsprozess auch den Beschäftigten, dass Sicherheitsthemen niemals „erledigt“ sind, sondern kontinuierliche Aufmerksamkeit erhalten – ein Kernprinzip moderner Sicherheitskultur.
Rechtlicher und normativer Rahmen
Die Gestaltung des Evakuierungsmanagements in Industriebetrieben wird in Deutschland von einer Reihe gesetzlicher Vorgaben und Normen bestimmt, die als Mindestanforderung und Orientierung für Best Practices dienen. Zunächst verpflichtet das Arbeitsschutzgesetz (ArbSchG) in §10 den Arbeitgeber, erforderliche Maßnahmen für Notfälle zu treffen – hierzu zählen die Planung von Evakuierungen, die Bereitstellung von Alarmmitteln sowie die Bestellung von Evakuierungshelfern und Durchführung regelmäßiger Evakuierungsübungen. Die Arbeitsstättenverordnung (ArbStättV) konkretisiert diese Pflichten für betriebliche Räumlichkeiten: Nach §4 Abs.4 ArbStättV muss der Arbeitgeber dafür sorgen, dass bei Gefahr Beschäftigte sich schnell in Sicherheit bringen können – dies impliziert klar definierte Fluchtwege, Notausgänge und Alarmierungsprozesse. Ergänzt wird das durch die Technischen Regeln für Arbeitsstätten, insbesondere ASR A2.3 "Fluchtwege und Notausgänge, Flucht- und Rettungsplan", welche den Stand der Technik für Evakuierungsorganisation darstellt. Die ASR A2.3 gibt detaillierte Hinweise zur Anzahl und Breite von Fluchtwegen, maximalen Fluchtweglängen, baulichen Anforderungen sowie zur Erstellung von Evakuierungsplänen und Durchführung von Räumungsübungen. So fordert sie u.a. eine jährliche Begehung der Fluchtwege und empfiehlt regelmäßige Übungen zur Überprüfung der Pläne. Auch wird betont, dass Fluchtwege dauerhaft freigehalten werden müssen – das Blockieren von Notausgängen ist ausdrücklich verboten. Daneben existiert die ASR A1.3 "Sicherheits- und Gesundheitsschutzkennzeichnung", die sicherstellt, dass Rettungswege mit einheitlichen, normgerechten Piktogrammen ausgeschildert sind (in Übereinstimmung mit internationalen Normen).
Wesentliche Normen auf europäischer und internationaler Ebene wurden in das deutsche Regelwerk integriert. DIN EN ISO 7010 legt etwa die standardisierten Sicherheitszeichen fest (z. B. das grüne Piktogramm für Notausgänge), damit Beschilderungen weltweit verständlich sind. DIN ISO 23601 definiert die Anforderungen an Flucht- und Rettungspläne: welche Inhalte sie mindestens enthalten müssen (Gebäudegrundrisse, eingezeichnete Fluchtwege, Notausgänge, Standorte von Feuerlöschern und Erste-Hilfe-Einrichtungen, Sammelstellen, Verhaltensanweisungen etc.) und wie sie grafisch zu gestalten sind. Das Vorhandensein aktueller, normgerechter Pläne ist in unübersichtlichen oder großen Arbeitsstätten verpflichtend. Eine weitere für viele Industriebetriebe relevante Norm ist DIN 14096, welche die Erstellung einer Brandschutzordnung regelt. Die Brandschutzordnung besteht üblicherweise aus drei Teilen (A, B, C): Teil A sind kurz gefasste Verhaltensregeln für alle Personen (z. B. „Ruhe bewahren, Feueralarm betätigen, Gebäude geordnet verlassen und zum Sammelplatz begeben“), Teil B richtet sich an Personen mit besonderen Aufgaben im Brandfall (Evakuierungshelfer, Brandschutzhelfer, Führungskräfte) mit detaillierteren Anweisungen, und Teil C enthält objektspezifische Angaben für Brandschutzbeauftragte und das Management. DIN 14096 gibt Aufbau und Aushang der Brandschutzordnung vor und stellt sicher, dass diese regelmäßig geprüft und angepasst wird. Dadurch wird gewährleistet, dass Verantwortlichkeiten und Abläufe schriftlich fixiert und allen bekannt sind, was im Evakuierungsfall absolute Klarheit schafft.
Neben diesen arbeitsstättenbezogenen Regelungen gibt es Spezialvorschriften für bestimmte Branchen. Etwa unterliegt ein Chemiebetrieb oder Raffinerie der deutschen Störfall-Verordnung (12. BImSchV), die auf der europäischen Seveso-III-Richtlinie basiert. Sie verpflichtet Betriebe mit hohem Gefahrenpotenzial, ausführliche Alarm- und Gefahrenabwehrpläne zu erstellen und regelmäßig zu üben, wie Mitarbeiter und auch umliegende Anwohner im Ernstfall geschützt bzw. evakuiert werden. In solchen Betrieben sind behördlich überwachte Notfallübungen im Turnus von meist ein bis drei Jahren vorgeschrieben, und es müssen Warnmittel (Sirenen, Lautsprecher) für die Umgebung vorhanden sein. Weitere branchenspezifische Vorgaben finden sich z.B. in den Unfallverhütungsvorschriften der Berufsgenossenschaften (DGUV Vorschrift 1 fordert allgemein, dass für Brände und andere Notfälle zuständige Personen benannt werden und Evakuierungen organisiert werden) oder den Bauordnungen der Länder für Sonderbauten. Europäische Standards fließen über EN-Normen ein, und auf globaler Ebene geben Normen wie ISO 22320 (Notfallmanagement – Anforderungen an die Einsatzleitung) einen Rahmen für effektives Vorfallmanagement, während ISO 45001 (Arbeitsschutzmanagementsysteme) fordert, Notfallszenarien im Managementsystem zu berücksichtigen und regelmäßig zu proben.